Buying a Tape Machine: An 11-Point Checklist — from “Midnight Bob” Shuster
Tape is still in high style in the audio world. Like a 1957 Corvette or a standup Pac Man machine, some technical pleasures never go out of fashion.
Although 99% of today’s audio facilities have a DAW as the center of operations, an element of analog tape processing remains a welcome element in a large number of studios.
While many engineers are content to approximate the sound with the wide array of tape-emulating plugins currently available, there’s no shortage of recordists willing to go hard-core with an actual tape machine on hand.
The problem for engineers, producers, studio owners, and archivists who have their heart set on obtaining a tape machine – whether it’s their first or is complementing one or more machines already in-house – is that there are virtually no new models on the market. Save for the Otari Mx5050 MKiii, which is still being made on a limited but costly basis, people who want/need tape will have to obtain a used machine.
So how do you know if that shiny Studer A827 24-track 2” machine that you’ve just discovered for sale on Craig’s List is your dream machine, or a lemon?
One man who can tell quickly is “Midnight Bob” Shuster of Long Island-based Shuster Sound, who stands among the country’s most experienced audio techs. A professional maintenance engineer since 1975, Shuster kept all the gear humming at top NYC facilities including the Power Station, Media Sound, Record Plant, Electric Lady, Sony Studios, Pomann Sound, Avatar, NBC, and many more.
Today, Shuster’s clientele has grown to include an ever-expanding list of solo studio operators and engineers, as well as radio stations, who count on him to keep their analog gear running strong. Tape machine repair and maintenance can account for several of Shuster’s house calls each week, and while some of the newly-obtained Ampex, Otari, Studer, MCI and Scully machines he sees are running clean, others would be more useful as retro coffee tables.
“NYC remains a hotbed of recording, and tape is enjoying a renaissance,” Shuster says. “I’m seeing that up-and-coming engineers, the old-timers, and everyone in between are discovering ways to combine the new and old. And people are saying, ‘I want an analog tape machine, because I know that it can make my record sound better.’”
If you’re thinking of adding a vintage tape machine to your palette, then you need to know what potential pitfalls to watch out for while shopping. Useful maintenance tips are here as well, for those who take the plunge.
Be sure to equip yourself with this essential checklist, as explained by Bob Shuster:
It’s the Heads
A tape machine is only as good as the condition of its tape heads.
Tape heads are the devices responsible for directly recording and playing back the magnetic pattern to or from the tape. Just like a phonograph stylus on a vinyl record (OK, I’m dating myself here), or a microphone, they are transducers. If a head is corroded, rusty or pitted, it will have an effect on the ability to accurately transfer the sound to a magnetic imprint on tape.
Heads can either be relapped or replaced. Relapping is a process of returning the original contour to the face of the head. This is done through a highly refined process of compounding and polishing the head by a skilled specialist.
Re-lapping is obviously the most economical choice, and most headstacks can be relapped between one and three times (depending on the amount of wear on the heads each time). A good test for a worn head is to take your fingernail and run it along the upper or bottom edge of the head — if you can feel a ridge or your nail catches on a ridge, it is a good idea to have it inspected for possible relapping. The exception to this would be an “undercut head” which actually has grooves cut just above the top and bottom of the head cores to help reduce edge wear and protect the tape.
To those unfamiliar with headstacks, it is difficult to explain the differences between head wear and intentionally undercut heads, but it is most easily explained that the undercut head has wide machined grooves which is easy to see. If the head is not undercut, it should have a completely smooth surface and your nail should not catch on ridges. You may also see uneven patterns across the face of the head. Badly worn heads will have grooves at the top and bottom where the tape has travelled and causes level inconsistencies and can even damage the tape.
Another indication of bad heads is that they may not play or record at all and they may be worn beyond what relapping can repair. If you’re not sure about you’re seeing, call somebody in to do an evaluation. If you’ve purchased the deck already, have the heads taken off the machine and send them down to John French of JRF Magnetics in New Jersey – he’s the legend as far as saving tape heads. For illustrations and further information about heads and relapping, visit JRF Magnets at http://www.jrfmagnetics.com.
If it’s too late for relapping, then replacement heads are the ultimate step, but that’s considerably more expensive.
The Tape Path
Next, take a look at the tape path: the reel spindles, incoming guides, impedance rollers, capstans, tach roller, tension arms/rollers, lifters and pinch roller.
Reel Spindles: hold and secure the reels of tape on the machine
Incoming and Outgoing Tape Guides: provide proper positioning of the tape across the heads
Impedence Roller: smooths the tape as it comes off the reel before reaching the heads (See “Image 1” in the gallery following the article)
Lifters: guides that pull the tape away from the heads in fast wind modes to prevent unnecessary wear on the heads. Lifters can also be released for fast wind audible cue. (See “Images 2 & 3” below)
Capstans: provides the precise speed to drive the tape past the heads. Rotational speed and diameter of capstan shaft determines the speed. Most capstans shafts have a dull finish. When they become too polished or shiny, they may cause tape slippage and speed errors. The capstan should be able to be rebuilt or refinished by a specialized motor rebuilding service. One such company is MDI Precision Motor Works, visit at http://www.precisionmotorworks. (See “Image 4 & 5” below)
NOTE: There are two disclaimers to the polished finish “rule” about capstans. There ARE some designed to be polished or shiny. The best way to determine if your machine’s parts were designed as such is to check the entire length of the shaft. If it is uniformly polished, it is probably designed to be so. Other capstan shafts are made from ceramic material and wear out very slowly, if at all. They are white in color.
Pinch Roller: rubber roller that provides proper tension to the tape against the capstan, permitting tape to draw off the supply reel and past the heads at a constant speed. If the pinch roller becomes gummy or cracks, it should be replaced or rebuilt. One of the rebuilding companies I use is Terry Rubber Rollers, at http://www.terryrubberrollers.com.
Tach Roller: (found on more advanced machines) Used for tape read-out/time counter and also monitors the direction of the tape and its speed for transport control. (See “Image 6” below)
Rotating components in the tape path (guides, impedence rollers, tac rollers, lifter rollers) can have noisy bearings. To test for this problem, you should put a recorded tape on the machine and listen. If you detect noisy bearings, they may need to be replaced. Luckily, many of these parts are shared by a wide range of machines, so they are readily available through many companies that make bearings.
The Motors
In a tape machine, you’ve got the capstan motor, supply motor, and takeup motor.
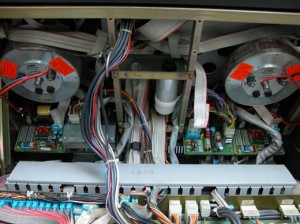
From a Studer A820: The underside of the reel motors, with an MDA motor driver and electronics below.
Reel Motors (Supply & Take Up Motors): controls the reel play out of each reel and provides proper tension across the tape path and heads. It’s easy to tell if you have problems here. They either work or they don’t. If you encounter motors that do not work, they could have worn out or burned out. Either case, they need to be replaced or rebuilt. On newer decks, the motors are driven by a motor drive amplifier (MDA, for short) and this amplifier can fail, preventing the motor from operating. The only way to make this determination is through component level troubleshooting by a skilled technician.
Capstan Motor: the most critical motor in the machine. If it is not working properly, the tape will not move properly across the heads, you may hear flutter or other unusual noises when listening to a tape. The best tests include using an alignment tape to distinguish if the tones are steady. Using a piano recording is also a critical way to test for flutter.
Keep in mind that if one of the motors isn’t turning, the motor itself may not be bad – it may be the circuitry. The drive electronics may not be happy. The only way to test for this is through component level trouble shooting performed by a skilled technician.
Other Rubber Parts
Rubber parts are prone to stretching, drying out and crumbling or even turning into a liquid black goo, depending on how they were treated. Urethane parts can turn into a white-colored liquid goo. This is particularly of note to those tape machines using the indirect drive of capstan. In other words, a machine that uses a motor to drive a belt/flywheel containing the capstan shaft. The belts are made of rubber and should be replaced if any of the conditions described above are present.
Some Ampex and Otari multitracks use a servo system that employs capstans only and no pinch roller. On these machines, the capstan rollers are made out of rubber or urethane and can experience the same problems described above. However, they can be rebuilt in most cases.
There are also some parts of braking that use rubber which should be checked, as well. Most machines do NOT use rubber brakes, but those that apply can be found under the deck plate by the reel spindles or motors.
Speed
Just to review the basics, tape machines record at different speeds, the higher the speed, the better the quality of the recording. The measure is IPS or inches per second of tape that passes across the record head. Obviously, the faster the tape speed, the more tape that is used to record the performance, so there are financial considerations in determining the speed at which you want to record.
Speeds range from 15/16ths IPS (which is only used for low quality voice recordings and logging) up to 30 IPS for the highest quality analog music recording and mastering. If you are doing any serious recording or mastering you will only want to record at 15 IPS or 30 IPS.
7 ½ IPS is the lowest speed considered for “professional” use, but it was limited in use. In the past, radio stations used it as a way to save tape and it was considered the top speed for home recording use. However, it was only used in professional audio recording for making dubs to give to clients to play at home or for radio station use.
There are machines that record at 1 7/8ths IPS and 3 ¾ IPS. Besides reel-to-reel machines, cassettes were recorded at 1 7/8ths IPS. The much maligned 8-track cartridge was recorded at 3 ¾ IPS and this speed was considered to be a good voice recording and background music recording speed for home reel-to-reel use.
Track Width
The wider the track, the quieter the tape and the hotter the signal that can be recorded onto the tape. The tape width determines the amount of tracks you can record on a tape and still maintain excellent quality.
Two-track recordings are stereo mix-downs and should be recording on either ¼” or 1/2” formats, depending on your budget.
If you are doing multi-track recording on an analog professional format, there are the following choices:
=1/2” four track
=1” eight track
=2” sixteen or twenty-four track
There are also semi-professional formats as follows:
=1/4” four track
=1/4” eight track
=1/2” eight track
=1/2” sixteen track
=1” sixteen track
=1” twenty-four track
There are some 1” two track machines used for mastering, but they are very exotic and extremely expensive to operate. They are specially modified headstacks installed on professional two track machines.
So, the faster the tape speed and the wider the tape, in general, the better the quality of the recording, but, also, the more expensive the cost of tape. At 30 IPS, a standard 2500 foot reel of tape will only provide a little over 16 minutes of record time. Depending on the width of the tape, the tape costs range from $50-300 per reel, or more. (Note: Tape costs fluctuate greatly).
Updates
On professional studio machines, manufacturers generally released updates to improve performance. Some lesser quality machines might also have upgrades if the original owner turned in the warranty card and paid attention to service update advisories.
For example, if you purchased a Studer A80 made in 1978, there were manufacturer updates up until the late 1980s, which included things as important as changing the heads, so you may be lucky enough to find a machine that has been updated on a regular basis.
At the big studios, such as Power Station, we would get calls in the Technical Maintenance Department from Studer, Sony, and Ampex letting us know of updates, “We have an update. Can we send a tech over to update all of your machines?” Everything would be kept in their files and the manufacturer kept track of which machines were eligible for updates and when. The update could be something as simple as a resistor value where they would say, “This update will make your deck sound better.”
You can check to see if a machine has been upgraded by looking for a little sticker in the machine which indicated the version. If it’s a later machine with microprocessors, then you can look in the service manual and it will say that this microprocessor was put in from “x” serial number to “y” serial number. Or you can check online, there are still websites that cater to these machines.
Some decks, like the Studer A820 (pictured) will provide the software version in the menu display when powering up.
Service records for machines are a rare commodity. The largest facilities kept logs for all of their equipment, but most of the analog reel-to-reel machines were taken out of service some time ago and most of those records are no longer available. Plus, many of the machines have changed hands a number of times and the current owners never thought to request any of the past service records or notes.
On rare occasions, you may be lucky enough to find that meticulous owner. I actually knew the Media Sound and Power Station machines individually, and have recognized one or two of the Media Sound machines when we’ve met again in a different studio, but that only comes from spending many years with my hands inside the guts of the machine.
Rebuilding/Restoration
Due to the nature of electrolytic capacitors, there is a tendency for them to dry out, resulting in degraded audio quality due to the fact that their values shift. Therefore, one of the currently popular topics is replacing these capacitors (“recapping”) in audio electronics and power supplies. I doubt that the manufacturers ever thought we would be still using some of this equipment over a period of more than 40 years, so the capacitors are just plain getting old.
Old microphone pre-amplifiers and consoles are very popular purchases today, and I spend a lot of time recapping them and the same thing applies to the electronics on analog reel-to-reel tape decks. These older workhorses are often in need of new electrolytic caps. So, when you are investigating the purchase of a machine, ask questions about whether they replaced any of the capacitors during routine or emergency maintenance. If not, you should budget for this expense.
Capacitors are components found on the circuit board inside the tape machine. Most people cannot check out the condition of the caps themselves because it requires test equipment to measure the value of each component.
There were some pieces of electronic gear that were known to have bad capacitors from the time they were new. But most of those capacitors will have already been replaced by the time you would acquire it second-hand, unless it was barely used.
Unfortunately, there are not many resources available to provide in-depth technical information about these vintage tape decks, consoles or other pieces of great gear since so many of the manufacturers are out of business, the machines were often custom-made for the purchasing studio, and they were often not widely produced. However, you can check out a few of the online discussion groups that people have created for individual brands: Studer, Ampex, Otari, Scully, and others.
If you know that a piece of electronic gear has not received any maintenance in the past 20 years, you should count on having to replace capacitors.
Basic Maintenance
Say you take the plunge and buy a tape machine, or you’ve already got one, there’s day-to-day maintenance you should do. I don’t mean pulling out the test equipment and doing an overhaul – just regular maintenance associated with normal usage.
For keeping the tape heads and the tape path clean, use 91% or better isopropyl alcohol with Qtips – either wooden stick Qtips or regular Qtips. Dip your Qtip in the alcohol, clean the guides, the heads, the capstan. You want to keep your machine clean! Especially if you’re playing back a lot of old tapes with sticky shed problems. But then you may want to be baking tapes, which is a topic for a whole other conversation.
The heads should be demagnetized once a week if you are using the deck regularly. I recommend one made by R.B. Annis called the “Han-D-Mag”. You can find them on eBay or a Pro-Audio vendor like Sweetwater or John French at JRF Magnetics. The last time I looked they were less than $100 new. The instructions are on the package. It’s an easy DIY procedure.
The motors should be oiled from time to time….once a year or every six months, depending on use, using what the manufacturer specifies. DO NOT USE 3 In 1 Oil!!
Keep the outside of the machine clean as well. Use a damp cloth to remove dirt, dust, and grime. Cover the machine when not in use, but only when the power is off.
You should also purchase a MRL (Magnetic Reference Lab) Calibration Test Tape. This tape with tones on it allows you to setup your recorder to standard operating levels. If your tape is played on other machines that were setup with the test tape, it will playback correctly. You should record test tones on the beginning of your masters if you send them out for mastering, 1khz, 10khz, 15khz, 100hz and 50hz.
Tape Costs and Tape Types
One of the most frustrating things about analog recording in the past five or so years has been the lack of availability of magnetic tape, and the tape that is available is expensive. Right now, we only have two companies manufacturing magnetic tape. RMG, which is really now known as Zonal, is a company located in Holland, but manufacturing their tape in France. The other company is ATR, which is located right in the U.S. of A. in Pennsylvania, and is owned by Mike Sptiz.
The quality of the two manufacturers is similar, both are professional grade. But be aware that, historically, magnetic tape has been known to have a “bad batch” now and then. Most manufacturers will exchange bad product for new if you make them aware of the situation.
Tape can be reused multiple times unless it has been damaged or spliced. However, you do not want to re-record on tape that is sticky or shedding, which is a problem found with certain brands of tape. Some include Ampex 456 and 406 (the Quantegy 456 was generally OK), Scotch 226 was also notoriously bad for sticking and shedding.
Professional Support
Tape machines are complicated electromagnetic devices, which require servicing. Unless you know what’s going on in the machine, it’s best to call a pro. If you want something aligned, just call us. We’re here to keep the machines going, because no one is making them anymore.
Maintenance is a necessary evil – there’s not that much stuff out there that’s 20 years old that people want to use, but if it sounds good you’ve got to keep it going. Guitar amps are a great example of ancient technology still being made today.
So you need a tech guy to check out a machine beforehand and after you acquire one, and nine times out of ten the guys working on your tape machines can fix the rest of your equipment too. For mixers, Pultecs, limiters, you’re tapping into a lot of knowledge from these people. There’s not a lot of us, but we’re still around and brave enough to stay in this business!
Midnight Bob Shuster is located in Metro New York and can be found at http://www.shustersound.com.
Please note: When you buy products through links on this page, we may earn an affiliate commission.
Lou Holtzman
August 5, 2013 at 8:10 pm (11 years ago)24 trk on 2 will always remind me of the scully 1 inch 12 trk. A raging flop. Nothing like my 1 inch 8 trk head stack.
So goes 24 trk stack,nice but lacking.
Now,16 on 2 was the sound. Just what analog was all about.
Maybe I will pull that 24 out of storage and remove the 24 stack and put John French’s wonderful 16 stack back on.
Any of you kids no how to align a machine?
Lou Holtzman
EastSide Sound NYC
Lou Holtzman
August 5, 2013 at 8:14 pm (11 years ago)Oh, let us not forget the AES of 1979 ,TAH DAH, introducing the MCI 32 trks on 3 inch tape. Interns had to be physically fit to carry the tape reels. Oh, what a bizz.
Bob Shuster
August 6, 2013 at 7:05 am (11 years ago)The great MCI 32 track 3″ format that never happened. Saw that at AES in NY at the Waldorf Astoria Hotel. Had 3M mock-up reels with 3″ tape. We figured a 14″ reel would weigh in around 25 -28 pounds! Try and spin with that…try carrying it! MCI also invented a new speed for the format – 20ips! it never happened and wasn’t necessary to mention. There was 2″ 32 track Otari and Telefunken and the famous Stephens 2″ 40 track. They hung in there for a while, but never really caught on in the mainstream studio biz.
Gee Genet
August 8, 2013 at 4:46 pm (11 years ago)Glad to see someone putting a spotlight on tape machines.I still use my Otari Mx 5050 8Hd machine i bought new,a Mx5050 4track, and a studer Revox 2track for mastering.Great article!!!!!
Bob Shuster
August 8, 2013 at 6:44 pm (11 years ago)Hi Gee, Thanks for the nice compliment on the article! It’s about time something was said about this great format and give its proper due time in the spotlight. Glad you enjoy it!
Best, Bob Shuster
Timheile
August 21, 2013 at 12:14 am (11 years ago)Awesome article Bob….thanks so much. I used to work at the Record Plant in Sausalito with Manny:) went on to help put together the P&E wing of NARAS in later years:) Lou mentioned the 16 on 2…..you ever come across those? Would love to find one in good shape if you have any leads. Thanks again.
Bob Shuster
August 21, 2013 at 4:12 pm (11 years ago)You’re welcome, glad you enjoyed the article! Will keep a 16 track 2″ in mind for you when one becomes available.
Bob
Steve @ Sonicraft A2DX Lab
August 21, 2013 at 5:41 pm (11 years ago)Nice article, Bob! Great stuff. Hope you post this on your website where folks can find it indefinitely.
Alan Garren
August 22, 2013 at 12:29 am (11 years ago)Nice overview, so many new people buying these great machines, So little knowledge in circulation among the new prospective buyers.
One item however, RMG is now made in France outside Paris by Pyral, I have had tape from the new plant and it has performed well. I don’t know about Zonal being in business, although Canford still list it in their catalogue, no price I could find though.
Playground estudio
October 14, 2013 at 3:15 pm (11 years ago)Great article Bob!
We have a Studer 16ch, 2″ A80 MKI running with Clasp in our studio @ Madrid.
Great sound!
All caps were refurbished and had a complete coming back to life by
Thomas Lefevre in France.
Very good professional and nice guy.
Thanks for all the info.
fmdcer
December 14, 2014 at 2:15 pm (9 years ago)Hello Bob, thank you for your posting your informative guide. It was not a top-of-the-line machine but one that I could afford as a teenager: a Roberts 771X (transistor). I enjoyed using it for many years but eventually had to sell it (broke my heart) as I was unable to source replacement heads as they were metal. I don’t know when the more popular glass-ferrite heads came out but the metal heads were the downfall of this 66 lb boat anchor. Yet, it was a remarkably solid and accurate 4 speed machine (1 7/8, 3 3/4, 7 1/2 and optional 15 ips). I dragged that thing to my band practises and shows. Before the quality dergaded any further, I copied most everything to cassette and finally to computer. I am now looking for another r2r deck as I’ve really missed having a machine for some +30 years now, time to get another one…maybe an Akai…
Ben from Canada
Idiot
July 31, 2015 at 6:03 pm (9 years ago)I was exactly what my DISQUS name states, when I gave my deck to Bob for repair. After month of broken promises I got it back in the same state as I brought it in. Broken. At least he did not charge me for storage.
Bob Shuster
September 7, 2015 at 9:04 am (9 years ago)?